Metallurgical Technologies, Inc.
Case Study: Analysis of a leaking diesel engine oil cooler
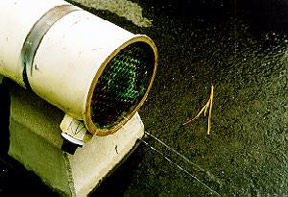
A leaking oil cooler that led to damage of a large diesel engine was analyzed to determine the cause of the leak. The heads on each end of the boost cooler were cut off so that the tube openings and tube sheets could be observed during leak testing. The shell side of the boost cooler was pressurized with water to examine for evidence of leakage. Two pin-holes were identified in the tube sheet.

The leaking tube sheet was cut away from the boost cooler. A close-up view of the pin-holes are displayed in this image.

The surface at the edge of the pin-hole is presented at a higher magnification using an SEM. The surface exhibits erosion damage and evidence of intergranular corrosion.

An axial cross-section was taken through a relatively non corroded area of the tube sheet and is displayed at low magnification using an optical microscope. The cross-section exhibits two braze layers that bridge the gap between two adjacent tubes.

The cross-section through the edge of one of the pin-holes is displayed at low magnification. Note that the outer tube sheet braze layer and most of the inner layer is missing.

Another axial cross-section was taken through a shallow (partial) pit in the tube sheet surface.

The pit location from the previous image is presented here at a higher magnification. The dark gray area in the outer braze layer is oxidation corrosion products of the outer braze layer. EDS analysis of corrosion products found down in the inner layer identified chlorine in the corrosion products.
CONCLUSIONS:
Results indicate that the boost cooler exhibited two pin-hole leaks in one of the tube sheets due to corrosion of the braze/solder filler used in tube sheet construction. The top braze layer exhibited general uniform corrosion. Once the inner copper braze layer was exposed, corrosion accelerated resulting in pitting. High concentrations of chlorine were found in the corrosion deposits at the pin-holes. Chlorinated flux, used during brazing, was identified as the source of corrosive material. The use of a non chlorinated flux was recommended.
Forensic examination of a failed component can prevent recurring failures, help with preventive detection, and suggest remedies. If you have a component failure that you would like investigated, just take a moment to fill in our information request form and we'll gladly give you an estimate.
Click here for more Product Details from
Metallurgical Technologies, Inc....