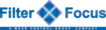
Contact Details:
Filter Focus
Germiston Motor City C7-C8
Jack Rd
Germiston
Gauteng
1402
South Africa
Tel: +27 (0)10 449 6414
Alt. Tel: +27 (0)64 960 3435
Send Enquiry | Company Information
Company Helps Reduce Client’s Carbon Footprint
Company News Wednesday, August 1, 2012: Filter Focus
Wear control and filtration specialist Filter Focus South Africa says it has assisted in lowering the carbon footprint of its customers through a meticulous oil-filtration and dehydration process using its vacuum dehydrator and oil purifier.
Filter Focus COO Craig FitzGerald states that the companies have become more aware of their carbon footprints as environmental responsibility has become more prevalent throughout various industries worldwide.
“Industries are more conscious of the negative impact their operations have on the environment. Carbon credits have become a valuable and tradable commodity,” he adds.
Further, he explains that vacuum hydrators assist in the removal of all water, gases and acids in oil, which have a negative effect on the eventual lubrication process.
“Water and other pollutants affect the oil’s base stock, encourage oxidation, and increase viscosity and foaming,” says FitzGerald.
The pollutants in oil can also cause corrosion by etching metal, through fluid breakdown, abrasive wear in hydraulic components, a reduction in the lubricating properties of oil and addictive precipitation.
“Filter Focus’s Vacuum dehydrator removes all water, gases and acids from lubricating oil, has high-efficiency demulsifying properties, a self-contained, fully automated one-touch control system, and also revives oil without the need to shut down,” he says.
Vacuum dehydration removes all three states of water in oil- free, emulsified and dissolved. It also removes free and dissolved gases.
“Wet or emulsified oil is drawn into the vacuum system.
“The first chamber is a quiet zone that leads to thermostat-controlled heaters and, from there, the oils move into the vacuum separator under negative pressure and low-humidity conditions,” he says.
This produces the best environment for quick and effective evaporation of dissolved water and gases at 40°C.
“All vapour and gases enter the chiller or condensation unit and are released into the water receiver. Cleaner, drier oil is passed back to the oil tank.
“Depending on the volume of water contamination, multiple passes are sometimes required to achieve target dehydration levels,” FitzGerald points out.
He adds that the process is completed through a customer-specified filter.
“We have had good results separating free and heavily emulsified water from lubrication oils in various environments. The key to good separation efficiency is the degree of vacuum and results down to 60 parts per million are achievable,” he states.
The benefits of vacuum dehydration include lower engine friction and wear, and longer engine and lubrication life.