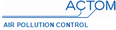
Contact Details:
ACTOM Air Pollution Control
3rd Floor, Cresta Junction, Block A
Cnr Beyers Naude & Judges Avenue
Cresta
Johannesburg
Gauten
2118
South Africa
Tel: +27 11 478 0456
Alt. Tel: +27 11 478 9765
Fax: +27 11 478 0371
Send Enquiry | Company Information
ACTOM Air Pollution Control on track with emissions control contract for Xstrata’s Lion Ferrochrome
Product News Thursday, February 28, 2013: ACTOM Air Pollution Control
At the end of February 2013 ACTOM Air Pollution Control was halfway with erection of the first of three bag houses in its current contract for the control of emissions from the new rotary dryer and two new kilns that form part of the Phase 2 smelter expansion project at Xstrata’s Lion Ferrochrome complex near Steelpoort in Mpumalanga.
The reputable Johannesburg-based company was awarded the multimillion rand contract – the largest it has won in its 44-year history – in late-2011 for completion in late-2013.
“The total package manufacturing is 85% complete, close to 50% of all equipment and other materials have been delivered to site and the main components of the rotary dryer bag house have been erected, with the remainder due to be installed by the end of March. We have also started erecting the bag house for Kiln C,” commented Gerard Pretorius, ACTOM Air Pollution Control’s Marketing & Sales Manager.
The Lion Ferrochrome Phase 2 expansion will increase the capacity of the smelter complex by 360 000 t per annum, bringing its total annual capacity to over 2,3-million t.
The emissions control contract being undertaken by ACTOM Air Pollution Control comprises design, manufacture, supply, installation and commissioning of:
• Two suction reverse air bag filter bag houses for fume and dust extraction in the two rotary kilns, Kiln C and Kiln D.
• A suction reverse air bag filter bag house for fume and dust extraction in the rotary dryer.
• Seven pulse jet bag filters for de-dusting in the mill and pre-wetting operations.
• Ducting and materials handling equipment serving the above installations.
• Fans and stacks.
Said Pretorius: “The combined air-moving capacity of the two reverse air bag houses for the rotary kilns and the rotary dryer will be 1,4-million m3/hr and the total capacity of the seven pulse jet bag filters will be 75 000 m3/hr.
“All the bag filters are thermally insulated. Those in the rotary kiln bag houses will operate in temperatures of around 140 degrees C, while the bag house for the rotary dryer will operate in an average temperature of 180 degrees C.
“Cleaning of the bags is done off line via automatic PLC-controlled dampers and cleaning of each compartment is carried out while the rest of the compartments are in operation. Maintenance work is done on line by isolating each compartment concerned, which is achievable despite the high operating temperatures because the compartments are independent modules.”
ACTOM (Pty) Ltd is the largest manufacturer, repairer and distributor of electro-mechanical equipment and provider of turnkey solutions in Southern Africa, employing about 7 500 people with an annual order intake in excess of R7.5bn. It is a black empowered company with 42 operating units, 43 production, service and repair facilities, and 36 distribution outlets throughout Southern Africa.
ACTOM holds numerous technology, distribution and value added reseller agreements with various partners, both locally and internationally.